lean production and quality management Notes
Lean production and its features
Lean production is a process of production in which all forms of wastage are eliminated to pull down the financial costs of wastage (wastage of raw materials, human effort, time and energy) to achieve greater production efficiency.
Features of lean production
- Waste minimization – All the business processes or techniques of production that lead to wastage or do not add value to the products, are removed.
- ‘Right first time’ approach – Business aims to produce zero defect products in the very first attempt by testing and checking the quality and condition of resources prior to production.
- Flexibility – Resources must be adaptable to the changing needs of the business.
- Continuous improvement – The production efficiency is increased on account of continuous improvement.
- Supply chain management (SCM) – It is vital for the business to manage the supply chain and the partners involved in order to avoid any mistakes and maintain the efficiency of production.
Methods of lean production
Kaizen
- Kaizen is a Japanese word for the philosophy of continuous improvement. Kaizen is made up of two words, ‘Kai’ which means change and ‘Zen’ which means better. Hence, Kaizen means ‘changing for the better’.
- There are small groups of employees who identify and manage the small changes (that aim at continuous change) and improvements in the processes, strategies or activities of the organization and not one-off large improvements (people in the organization resist large changes).
- Kaizen aims at quality (products) management to improve the productivity efficiency.
Just-in-time (JIT)
- JIT is a stock control method in which the stock is delivered as and when the requirement arises.
- JIT is a Japanese management philosophy that was developed by Taiichi Ohno (Toyota executive).
- The buffer stock (the predetermined level of stock that is kept as a precautionary measure for contingencies) is not required to be kept under this stock control system.
Kanban
- Kanban (Japanese word for visual card) is a lean production method used to achieve JIT production. It is based on actual orders from the customers and not the sales forecasts.
- Stocks are managed through a visual Kanban card system and each component or a type of inventory that is used in the production process is allotted an inventory number.
- Through the Kanban board, operatives are able to identify the quantity of the items required, time limitation for production and delivery, tasks that need to be done and the ones that have been completed, work-in-progress, etc. This helps them to place accurate orders for the supply of raw materials, visualize the workflow and identify the bottlenecks, complete the WIP and handle the management of the overall production process and the supply chain by limiting the excess stock from being piled up.
- Restaurants, automobile companies, etc. are some of the businesses which use Kanban card method for lean production.
Andon
- Andon is a Japanese audio-visual control system that indicates the status of an aspect of the production process (machinery/equipment, production line, work process, etc)
- The color-coded traffic light system is used to alert the supervisors about the status of the any production process or machinery/equipment on the production floor.
[Green = Normal operations in progress, Yellow = Attention will be required soon, Red = Immediate attention required (emergencies)]. - Signal boards, alarms, lights are used for the notification. Andon alert systems can be activated automatically or manually. The defects and other issues are monitored and addressed and then the process is re-started.
Benefits of Andon
- It is a simple communication tool that brings instant attention to any problem in the production process.
- It helps the supervisors to easily identify the problem and resolve the issue effectively.
- Any problem in any aspect of the production process does not go unnoticed and the andon system avoids creation of any other problem.
C2C design and manufacturing
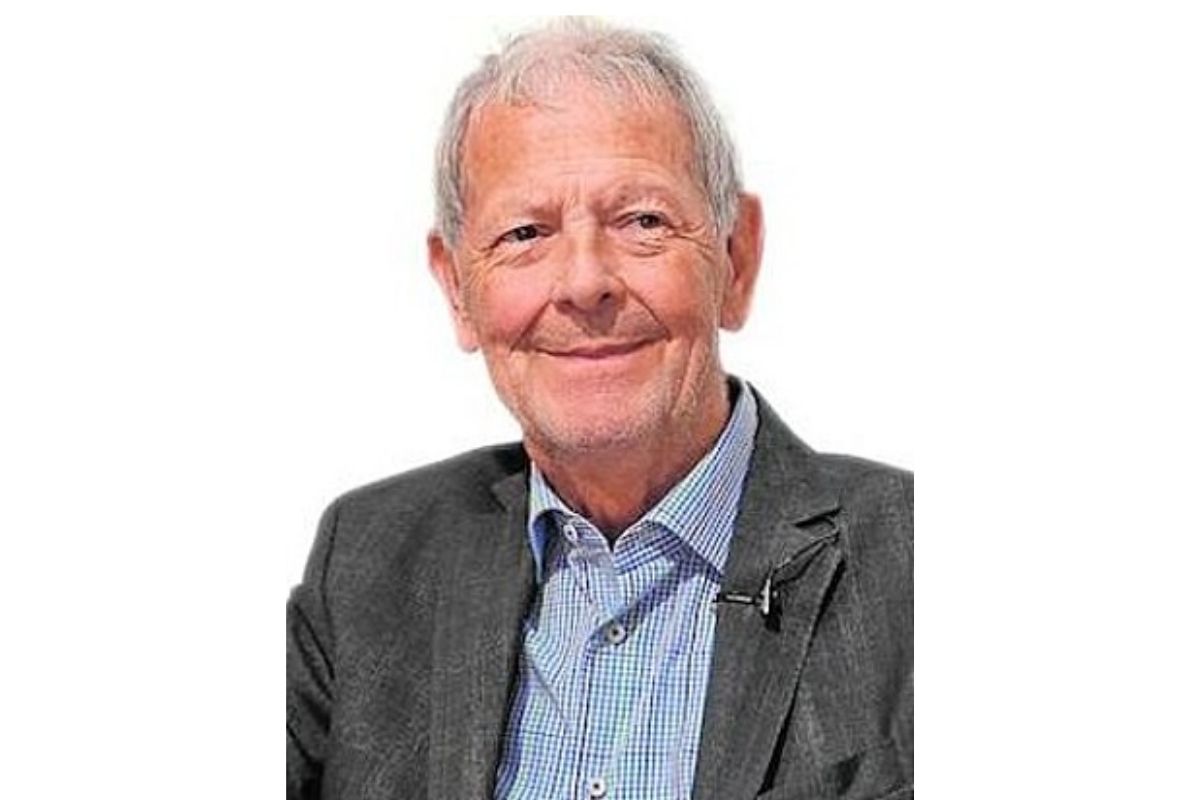
Cradle to cradle (C2C) is a sustainable production model/design that focuses on the use of natural processes of production where there is minimal or no wastage.
- Walter R. Stahel, a Swiss architect coined the term ‘cradle to cradle’ in 1971.
- The design and techniques of production used are such that there is use of environment friendly, non-toxic and biodegradable materials.
- For e.g.- Glass bottles are recyclable and so are the paper bags.
- Reduce, reuse and recycle are three ways in which any waste can be prevented.C2C philosophy is an important part of any company’s CSR (Corporate Social Responsibility) and results in increased costs for the company but enhances public image.
Quality control and quality assurance
Quality is the inherent aspect of the product that determines whether it meets the desirable standards and expectations of the customers or not. The products that do not meet the desired expectations of the customers are called sub-standard products.
Determinants of the customers’ perception of quality of the product
- Physical appearance and design – Customers find the product good if it has innovative design and attractive packaging (physical appearance).
- Image and reputation of seller/manufacturer – The reputable brands are always associated with the quality products in the minds of customers.
- Reliability and durability – The products that are highly durable (last for a longer period of time and reliable are considered to be of good quality.
- Solves the purpose or not – The product should fulfill the very basic purpose. If a customer intends to buy a laptop bag, then the first thing that would affect the choice is the availability of enough space to fit a laptop.
- Safety – The product is expected to meet all the safety standards.
- Customer service and after-sales service – A fine customer service during delivery as well as after the delivery of the product wins the customers.
Now, what is quality management?
Quality management refers to the function of controlling and managing the business activities and production processes in a way that products can meet the desired standards and the expectations of the customers. Due to increasing consumer awareness, increasing competition, developments in the competition law, and the increasing consumer incomes, maintaining the quality of the product has become the priority for businesses.
Two main categories of quality management are as follows:
- Quality control (QC) – It is the traditional way of quality management that involves inspecting, testing and sampling of the quality of any product. There are set standards and specifications for each stage that the product passes through right from the supply of raw materials to the output of finished products. In case of deviations, corrective actions are taken.
- Quality assurance (QA) – American poet Henry Longfellow said ‘’It doesn’t take a long time to do the right thing than to clarify why it was done wrong .’’ QA focuses more on ensuring that right things are done first time than rectifying the problems every time.
Advantages of quality control | Disadvantages of quality control |
|
|
The costs of producing substandard output (poor quality products) are as follows:
- Poor quality products give rise to customer grievances (reduction of demand). This damages the reputation of the business.
- Unsafe products can cause physical harm to the customers.
- The time and money are spent on rework and improvement of labor productivity. There is wastage of resources which leads to the increase in cost of production.
- The firm’s competitiveness and profitability are adversely affected.
Advantages of quality assurance | Disadvantages of quality assurance |
|
|
Four key phases of quality improvement (suggested by Professor W. Edwards Deming, the father of quality management) are as follows:
- Plan- Preparing a plan for revised processes to be used for quality improvement
- Do- The plan is executed and actions are taken
- Check- The performance is measured and monitored constantly to keep a check
- Act- In case of deviations, corrective measures are taken and necessary changes are added.
Common methods used to measure the quality
- Reject rate- More the rejection rate, the lower is the quality of the products that are produced.
- Level of product returns- Higher the level of products that are returned by the customers, less are the customers satisfied with the quality.
- Product recalls- If more products are recalled by the firm for corrections, the quality is at stake.
- Level of customer satisfaction- Good quality products and the products with least defects attract more and more customers since the customers are highly satisfied.
- Degree of customer loyalty- Customers stay loyal to a firm that produces quality products.
- Market share- Larger the market share of the firm, larger is the sales revenue and this takes place only when the customers receive quality products from a particular firm.
Quality management methods
Quality circles
- Quality circles are small groups of people (volunteers from various departments meet to discuss the product quality issues and suggest improvements).
- Unlike kaizen groups, the members also execute and manage the recommendations and the solution for quality problems.
- The term ‘Quality circles’ was coined by Professor Ishikawa in 1962.
- The meetings that are held are chaired by a senior manager.
Advantages of quality circles | Disadvantages of quality circles |
The morale of workers has improved because participation is quality management issues. There is an increase in the production efficiency and profitability since all aspects of the operations are covered in the discussion (quality circles). | Deviations are caused when some individuals are demotivated with the burden of extra responsibility. The possibility of conflict arises when people from various departments come together to work on quality improvement. |
Benchmarking
BPB (Best practice benchmarking) is the practice of comparing the business’s products, operations and processes with the market leaders in the same industry. BPB is the point of reference or comparison.
Two methods of benchmarking
- Historical benchmarking:
It is the practice of benchmarking that involves the comparison of a firm’s performance with its own past performance data. This is used for internal benchmarking in the organization. - Inter-firm benchmarking:
The performance data of the firm under the same performance indicator is compared with other firms belonging to the same industry.For instance, when the sales revenue of Airtel is compared with other telecommunication companies such as Vodafone and Jio, it is called inter-firm benchmarking.
Stages in the process of benchmarking
Types of benchmarking
- Performance benchmarking – It is used to benchmark the key performance indicators of a business. E.g.- sales turnover rate, labor productivity rate, etc.
- Process benchmarking – Used to benchmark the processes and operations of a business. E.g.- risk management or recruiting process, etc.
- Internal benchmarking – Used to benchmark different operations or functions in the same organization.
- External benchmarking – Used to benchmark the firm’s products or processes or performance with that of the best performing organization in the industry.
- International benchmarking – Used to benchmark the performance with that of the overseas organizations.
Benefits of benchmarking | Limitations of benchmarking |
|
|
Total quality management (TQM)
Benefits of TQM | Limitations of TQM |
|
|
TQM involves the participation of all the people in the organization in quality management. All forms of wastage in the business activities, functions, operations and processes are eliminated. The culture which incorporates TQM is called total quality culture.
National and international quality standards
There are various autonomous organizations that operate nationally/internationally to regulate the quality of the products produced by the organizations. The organizations which meet or exceed the set quality standards are awarded with quality symbols/logos on their products that assist them in the promotion of the products since the customers get assured of the quality of the products offered by the awardee organizations.
ISO (International Organization for Standardization)
- The most prominent global organization that regulates quality and one of the powerful NGOs in the world.
- Founded in 1947, based in Geneva, Switzerland.
- It is made up of 163 national quality standards bodies such as ASQ and BSI.
- Aim- To set a single set of quality standards to be recognized by all the customers and businesses.
- Businesses that meet ISO standards are ‘ISO 9000 certified’ or ‘ISO 9000 registered’.
Examples of national and international quality awards
- The CE Mark- European union’s award for products that meet health and safety standards.
- The ASQ award- The prestigious Malcolm Baldrige National Quality award is given by the American Society for quality for exceptional performance in the USA.
- The BSI Kitemark- The products that carry the British Standards Institution mark (UK) are of high quality.
- The Lion Mark- The mark is awarded by the British Toy and Hobby Association (BTHA) for the products (toys) that are safe and genuine.
Lean production, quality management and CUEGIS concepts
The quality management practices and action plans have to be constantly revised in the light of changing conditions that influence the operations of the business. Any external change such as change in the fashion and trends or internal change such as organizational culture/structure has to be considered to effectively create the TQM culture in the organization and attain lean production since quality management is a continuous process